AI in WMS is no longer optional; it’s becoming the backbone of intelligent, real-time operations. This big change happens because companies need to see things in real-time, make choices based on data, and have processes that can change when the market does.
In this article, we’ll show how AI is changing warehouse management in a big way, look at real examples of how it’s used, point out the clear benefits for companies of all sizes, and think about what’s coming next for smart warehouses.
What Is AI in Warehouse Management Systems (WMS)?
Fundamentally, AI in WMS is the use of artificial intelligence tools to imitate human decision-making and learning to change the daily operation of warehouses. Unlike conventional rule-based systems, artificial intelligence gives the power to evaluate huge datasets, react in real-time, and automate activities formerly totally reliant on human labor.
The scope of AI in warehouse automation goes far beyond simple mechanization. It blends cutting-edge technologies, including:
- – Machine learning: Learns from past patterns/ historical data to forecast future events/trends or form clustering SKU to streamline inventory and processes.
- – Computer vision: Let’s machines “see” and monitor products all across a warehouse.
- – Robotics: Deals with demanding or repeated physical operations, including picking, packing, and carrying products with great precision.
AI systems can understand patterns in their environment without a fixed and immutable script, which is a key part of distinct data from automated systems in distribution centers (i.e., AI adapts to the physical warehouse where stock is supposed to go, or being human-aware and making smart decisions based on it). When integrated into the warehouse system, AI enables adaptive responses to market shifts and operational challenges.
Core Roles of AI in Warehouse Management
The role of AI in warehouse management is more than just basic automation. Integrating Warehouse management AI features into daily processes allows companies to reach new peaks of agility, accuracy, and proficiency. Let’s take a look at how AI in WMS is transforming the way we do current core processes:
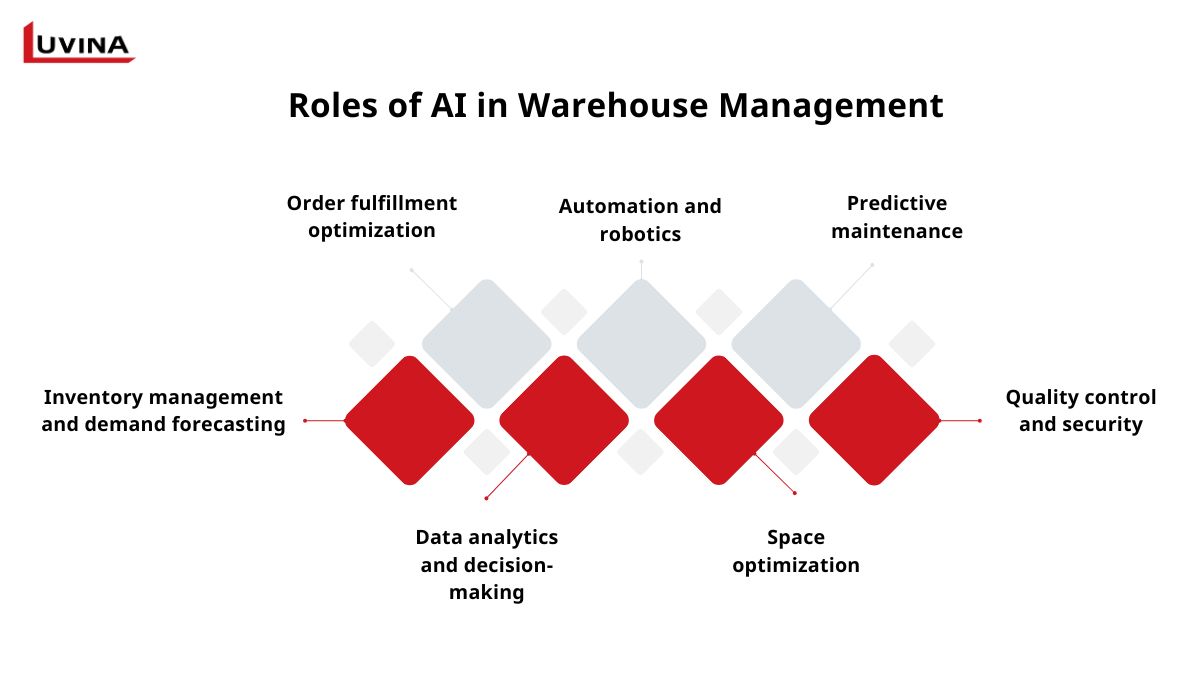
- Inventory management and demand forecasting
High-accuracy inventory needs predictions based on historical sales data, seasonal patterns, and market trends, powered by artificial intelligence comes from learning. This guarantees warehouses have ideal stock levels, therefore minimizing expensive overstocking or out-of-stock scenarios while yearlong customer satisfaction is maintained.
- Order fulfillment optimization
Smart algorithms pick routes, storage layouts, and orders to simplify picking and packing. AI greatly quickens fulfillment by lowering travel time and maximizing picking accuracy.
- Automation and robotics
Integration of robotics is among the most obvious components of Warehouse Management AI. Enhancing production, improving worker safety, and lowering human error, Autonomous mobile robots (AMRs) and AI-controlled picking systems take care of repetitive or complicated chores.
- Predictive maintenance
By contrast, rather than following rigid maintenance schedules, AI uses data generated by sensors in real time to anticipate failure. This saves unexpected shutdowns, increases the life of machinery, and decreases maintenance costs.
- Quality control and security
By measuring environmental conditions and automating inspections, artificial intelligence provides quality assurance by identifying defects that human checks could overlook. AI video monitoring also increases warehouse security by identifying anomalies or illegal activities more quickly than manual checks.
- Space optimization
AI algorithms process SKU dimensions, sell-through, and demand profiles in order to recommend optimal storage modules. This optimizes the use of warehouse space and facilitates faster item access, resulting in a better flow of operations.
- Data analytics and decision-making
The reason AI in WMS is so powerful is the ability to process data. AI is always processing operational data, identifying inefficiencies, monitoring KPIs in real time, and giving leaders actions in real time, allowing managers to use data to make decisions quickly.
Top AI Use Cases in Warehouse Management
The use of AI in WMS is opening up useful, high-impact uses that assist warehouses in running more sustainably, quickly, and intelligently. These are among the most revolutionary applications of AI use cases in warehouse management:
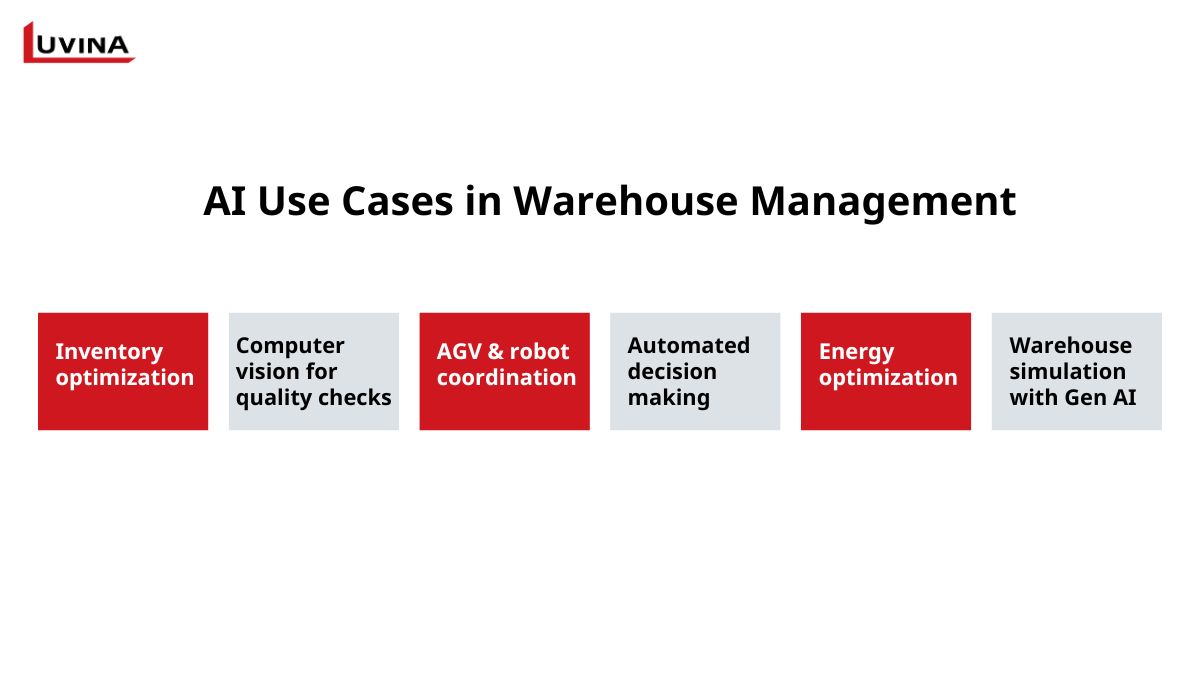
- Inventory optimization
AI’s predictive capability in controlling inventory levels is among its most priceless advantages. AI systems keep inventory at ideal levels by studying past sales trends and real-time demand signals, hence minimizing expensive overstocking or stockouts. Improved order accuracy and client happiness result from automated replenishment systems that guarantee goods are always accessible when needed.
- Computer vision for quality checks
AI in WMS that incorporates computer vision technology acts as a constant quality assurance inspector, with cameras and AI-based vision systems often identifying defects, mispicks, or packing errors on shelves or conveyor belts, and also providing time savings, the ability to reduce inaccuracies, and cuts on high perishable and wasted products.
- AGV & robot coordination
Autonomous Guided Vehicles (AGVs) and artificial intelligence robot systems reliably carry out routine transport, picking, and sorting tasks. Smartly coordinating many robots simultaneously increases throughput, lessens dependence on labor, and increases safety in a warehouse. This demonstrates that robotics is now an essential step forward for real-world AI use cases in warehouse management.
- Automated decision making
Systems with AI analytics sift through vast quantities of data to identify inefficiencies, assess risk, and recommend improvements that humans would not typically discern. Using this data-driven capability would improve matching along a continuum of resource utilization, inventory response, and even dynamic pricing. Natural language processing will allow AI to take advantage of valuable sources of unstructured data, such as chat logs, tickets, etc.
- Energy optimization
Current warehouses are now making energy efficiency the number one priority. AI tracks energy use in real-time and changes the lighting, HVAC, and equipment use when it detects energy use that should be reduced. Smart systems are able to track powering-draining patterns and automate the changes, saving costs while supporting sustainability initiatives.
- Warehouse simulation with Gen AI
Gen AI in warehouse management is one of the new frontiers. Generative AI’s elaborate simulation and scenario modeling can allow managers to visualize all the layouts they are trying, procedure flows, or peak-season demands, especially when they are about to make expensive changes in real life.
Benefits of AI in Warehouse Automation
Applying AI in warehouse automation is more than simply a technical improvement. It’s a strategic investment that delivers measurable benefits across your supply chain. Among the most significant advantages here:
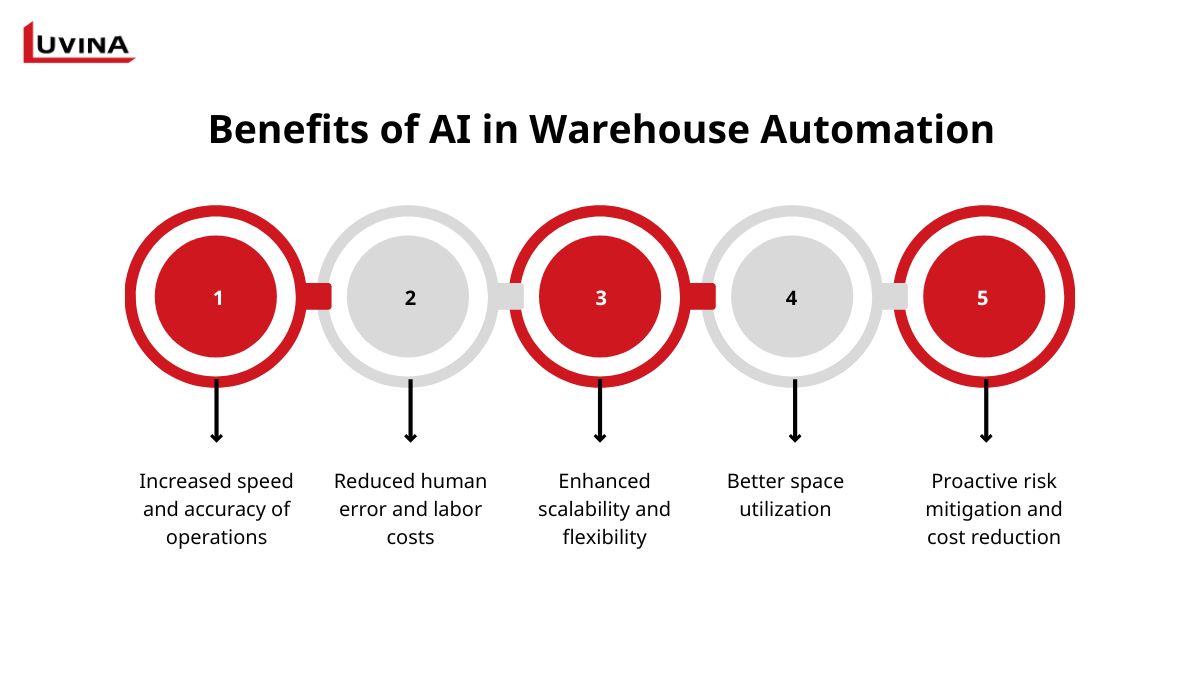
- Increased speed and accuracy of operations: AI-powered robots, predictive analytics, and smart routing greatly improve picking, packing, and shipping efficiency while lowering expensive mistakes by means of their increased speed and accuracy of processes. McKinsey reports that AI-powered tools may help warehouses gain 7–15% more capacity by revealing hidden daily slack, analyzing resource variability, and spotting efficiency improvements.
- Reduced human error and labor costs: Automating repeated tasks with the use of artificial intelligence reduces reliance on seasonal or temporary staff; furthermore, it lessens the likelihood of mistakes made during manual processes, resulting in significant cost reductions. Many logistics leaders report that AI in WMS helps lower labor costs by 20–40% and cuts errors in order processing, as robots and smart systems handle routine workflows with higher precision
- Enhanced scalability and flexibility: AI in WMS allows a warehouse greater ability to scale its functions up or down smoothly, as demands increase or market demands change without losing significant continuity.
- Better space utilization: Intelligent algorithms evaluate SKU data and turnover rates to maximize capacity and so better general warehouse flow by means of optimal storage layouts.
- Proactive risk mitigation and cost reduction: Artificial intelligence’s predictive capabilities will enable quicker identification of potential equipment failures, supply chain interruptions, or swings in demand, so appropriate actions can be taken that will minimize costs. According to Deloitte (2017), using AI and IoT for predictive maintenance can lower maintenance costs by up to 40%, increase equipment reliability by 30–50%, and cut downtime by half.
Challenges of Implementing AI in Warehouse Management
Although warehouse management AI offers evident operational benefits, using it has difficulties. Many companies undervalue the technical, economic, and human aspects of integrating AI in WMS for the first time. Some main problems to solve here are:
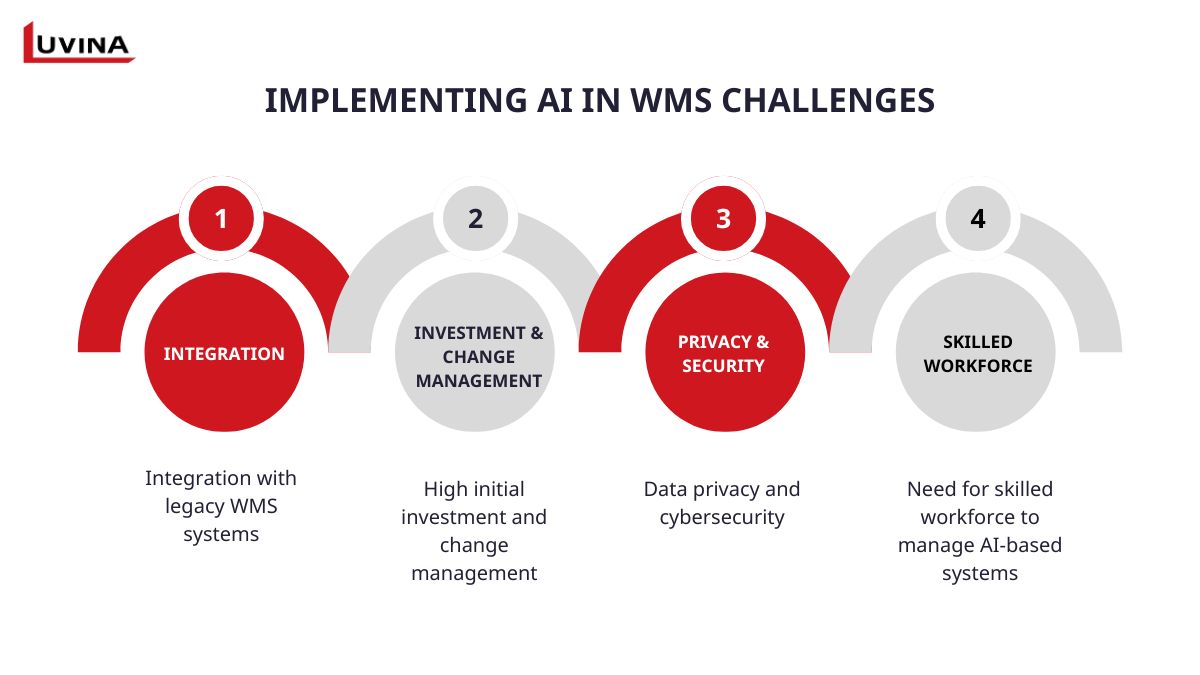
- Integration with legacy WMS systems: Integrating AI tools with WMS software that is no longer supported can be tricky. Integration should be smooth, to disturb as little as possible, and you still have data flowing from ALL your operations.
- High initial investment and change management: Rolling out AI technologies calls for a lot of upfront expense in new hardware, software, and IT infrastructure. Companies need to go beyond the budget also control internal opposition to change and offer training to enable teams to adjust.
- Data privacy and cybersecurity: Managing extensive sensitive operational data can only be done successfully with the assistance of artificial intelligence; therefore, data security and cybersecurity are crucial. Without the highest levels of protective security, warehouses could either break compliance regulations or create significant data breaches. The layers of defense before that occur are strong encryption, access controls, and clear policies for governance.
- Need for skilled workforce to manage AI-based systems: Need for skilled workforce to manage AI-based systems: As more tasks are automated, the need for qualified labor to use, understand, and communicate with AI systems will multiply. Developing this talent pool requires lifelong learning and a culture that embraces the very human qualities of innovation.
How to Implement AI in Your Warehouse Management
Adopting AI in WMS successfully involves following a straightforward, step-by-step plan that suits your particular company objectives. Key actions to assist you in properly implementing artificial intelligence in your warehouse operations are listed here.
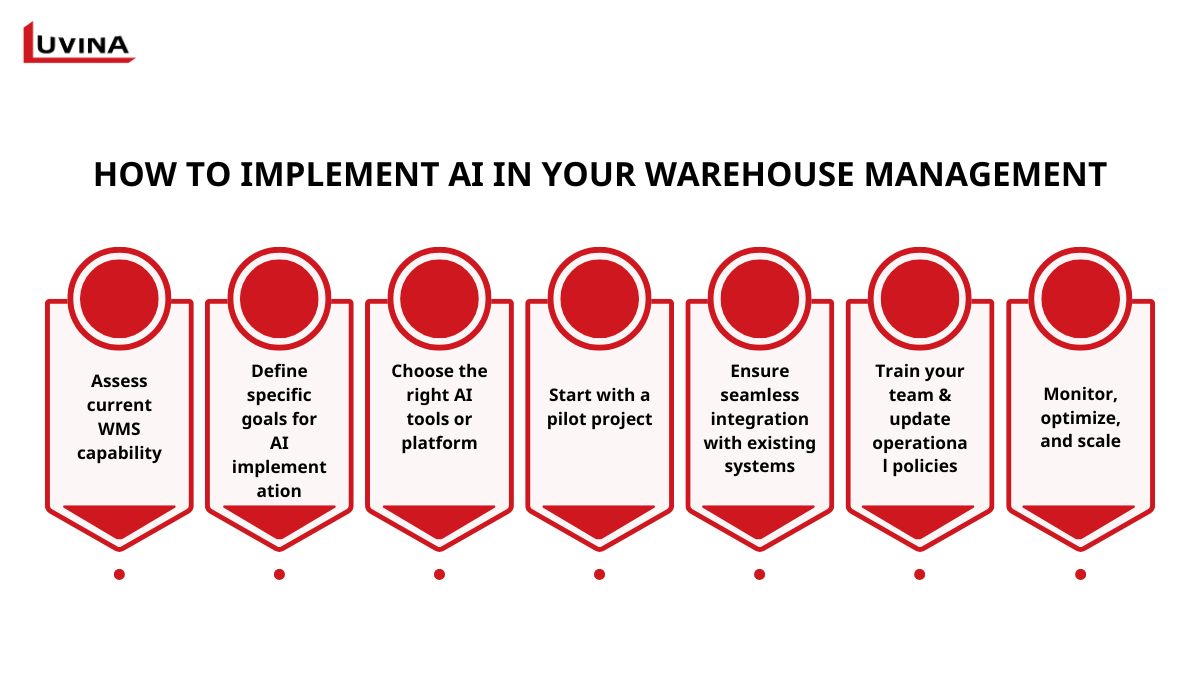
1. Assess current WMS capability
Start your artificial intelligence path by thoroughly examining your present operational processes and warehouse management systems. Find current strengths and flaws, identify inefficiencies, and get ideas from personnel handling daily activities. Knowing your current skills and constraints will give a strong basis to decide where artificial intelligence might be most properly incorporated and what changes may be required for a simple transition.
2. Define specific goals for AI implementation
Before rolling out AI tools, clear goals that are measurable and support high-level company goals must be established. If you don’t know what these business impacts are, whether for faster order fulfillment, lower operating costs or better inventory accuracy/quality control, then you simply don’t know what you don’t know. Think about the biggest problems your warehouse is facing at the moment, and how artificial intelligence could solve them.
3. Choose the right AI tools or platform
Choosing the right technology is a crucial first stage in properly including AI in WMS. Start by investigating artificial intelligence solutions matching your particular requirements. Based on technical skill, track record, and platform integration ability with your existing systems, assess prospective suppliers. Consider running pilot projects with shortlisted companies to verify performance and compatibility before adopting a full-scale launch so as to reduce risks.
4. Start with a pilot project
Starting with a pilot project in an enclosed environment or in one warehouse before implementing artificial intelligence systems more widely makes sense. This approach lets you find problems early and make required changes with little disruption to your company.
Real-world testing helps you to guarantee that the technology is in line with your company’s needs while also giving insightful input from customers and stakeholders. Choose pilot systems first with known scalability so that successful pilots can rapidly grow to full deployment. Adopting warehouse automation calls for this deliberate measure to ensure that AI in warehouse automation is smooth and efficient.
5. Ensure seamless integration with existing systems
Making sure your current systems and procedures integrate seamlessly is a crucial need for effective artificial intelligence adoption in warehouse management. Avoiding interruptions entails matching new artificial intelligence technologies to already in use warehouse management systems, inventory databases, and operational procedures.
Collaborate with internal IT resources and technology vendors to resolve compatibility issues and establish clear integration paths. Beyond the benefits of maintaining business as usual, perfect data sharing and interoperability enhance the value and productivity of your AI implementation.
6. Train your team & update operational policies
Effective warehouse management AI adoption depends mostly on readying your staff to appropriately utilize emerging technologies. Create thorough training initiatives that expose staff members to the artificial intelligence technologies, their characteristics, and real-world advantages.
- – Develop users’ confidence and competence through the preparation of “training materials” (user manuals, interactive sessions).
- – Promote a learning culture to keep your team up to date on new trends in AI and best practices.
- – To complement AI-enabled workflows, revisit and amend operational procedures, ensuring smooth interactions of human workers with automated systems.
7. Monitor, optimize, and scale
Ongoing surveillance of AI-enabled systems is crucial for sustained success with AI in WMS. Implement strong tracking systems to regularly identify straightening gaps and opportunities for improvement. New data is collected, and AI algorithms are again and again updated with fresh data, country-specific conditions, and dynamic supply chain trends. Regular inspections and audits will help you make sure that the artificial intelligence tools still help you accomplish your business goals and that the tools provide actual benefits.
Conclusion
AI is developing quickly and offering solutions that warehouses can put into action right now. Beyond higher productivity, AI in WMS allows for more intelligent, more agile, and scalable warehouse operations.
Ready to future-proof your warehouse? Let Luvina Software help you implement AI solutions that bring real results: from demand forecasting to robotics integration.
>> Also read: Custom Warehouse Management System: How to Build Your Own WMS
Read More From Us?
Sign up for our newsletter
Read More From Us?
Sign up for our newsletter