Digital transformation in manufacturing has been and will continue to be a game-changer in every aspect of this industry, giving businesses a much stronger competitive advantage. According to a survey by McKinsey, digital transformation in the manufacturing industry can boost productivity by 10% to 30%, improve quality costs by 10% to 20%, and cut downtime by up to 50%. Despite these many benefits, only one-third of the businesses currently adopt digital manufacturing transformation. It therefore means that most of the manufacturing companies across the world are failing to seize key opportunities.
The slow adoption or missed opportunities in digital transformation often stem from a lack of the necessary knowledge and experience. To address this issue, in the article below, we will clarify the concept of manufacturing transformation, the challenges involved, real-world examples, and ways to build an effective manufacturing digital strategy.
What is Digital Transformation in Manufacturing?
Digital transformation in manufacturing is the process of replacing manual or paper-based processes with digital tools and automation technologies to increase business value. Key goals of digital transformation for manufacturing companies often include:
- – Cost optimization
- – Enhanced quality and compliance
- – Improved sustainability
- – Boosted productivity and employee retention
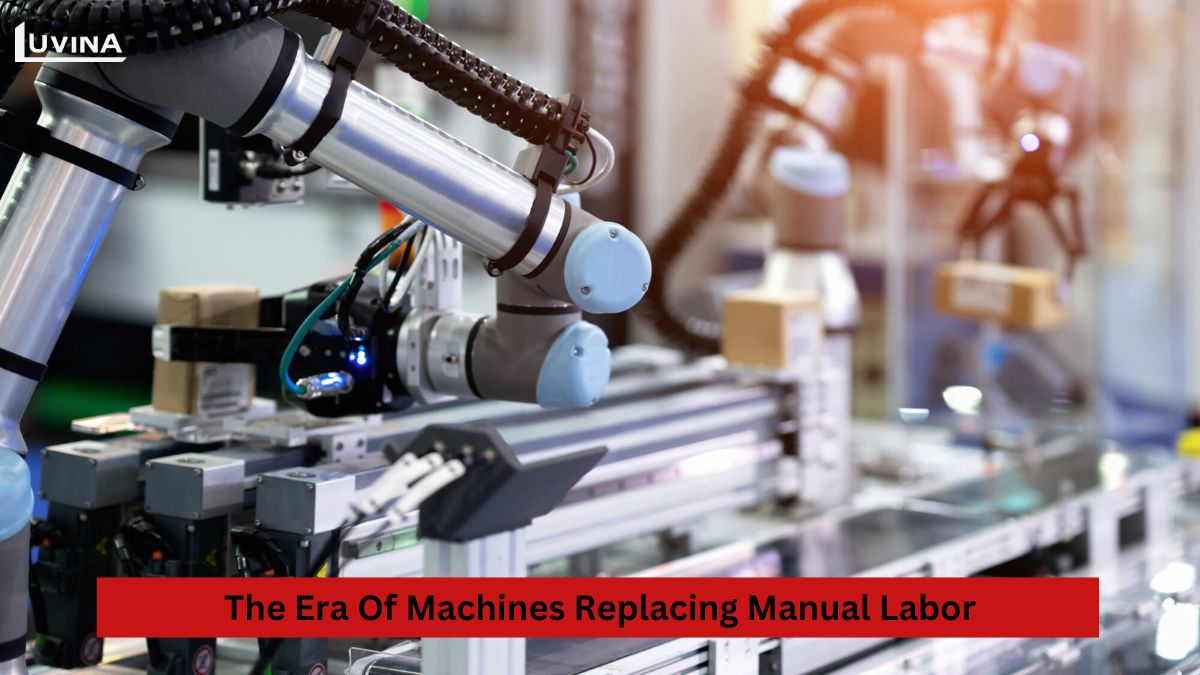
To achieve these goals, the manufacturing industry digital transformation typically involves support from various modern technologies such as the Internet of Things, manufacturing analytics, AI and machine learning, activity tracking, paperless manufacturing solutions,…
Digital transformation, being a broad business strategy, can be applied across industries, creating breakthrough opportunities in digital technology. More specifically, digital transformation within manufacturing is extremely instrumental for companies in an effort to maximize revenue, reduce costs, improve quality, and make them more flexible.
Challenges of Digital Manufacturing Transformation
Every development and innovation comes with challenges, and digital transformation in manufacturing is no exception. Below are some of the main challenges that manufacturing companies need to face and overcome to effectively implement new digital technologies.
1. Alignment in digital transformation strategy
Developing a digital transformation strategy for manufacturing requires regular alignment to ensure that the transformation progresses smoothly. An effective strategy aligns with business goals and creates measurable value. A well-aligned strategy makes digital transformation easier to succeed and more sustainable over time.
2. Data management
Data is at the core of many digital transformation initiatives. However, for many companies, especially large or long-established ones, data is often isolated, unusable, or inaccessible, presenting one of the biggest challenges in digital transformation in the manufacturing industry. Effective data management enables proper accessibility, which is key to unlocking advanced digital transformation efforts. It requires understanding data storage systems, accessing data, and ensuring data connectivity and validity.
3. Change training and employee engagement
Most successful digital transformations in manufacturing processes involve both employee and leadership participation. Employees need to feel ownership over the transformation, not as if they are simply fulfilling an executive mandate. For a successful digital strategy for the manufacturing industry, it is essential to build and nurture a culture where employees feel heard and their feedback serves as the foundation for innovation and change.
The transition to automation requires the acceptance and agreement of the workforce
As a leader, you must also clearly communicate to employees why these changes are happening and what digital transformation in the factory means for the business. Consistent and effective change management over the years, along with supportive training and skill development programs, is also vital.
4. Choosing the right technology partner
For a successful smart factory digital transformation, support from external providers and expert consultants is crucial. However, finding reliable partners is not always easy. Beyond cost considerations, it’s important to evaluate if the partner has suitable technologies, and expertise in the manufacturing sector, aligns with your values and innovation goals, and can scale with you over time. Choosing the right technology partner not only increases your project’s chances of success but also provides opportunities to work with industry-leading experts and establish a long-term partnership.
5. Selecting the right technology to invest in
Choosing the right technology to invest in is another major challenge in digital transformation in the manufacturing industry. Constant innovation can give you an advantage over competitors, but it’s not enough. What matters most is whether you have tools that are well-suited for your work and can adapt and scale with your business. Investing in the right technology equips you with essential tools to optimize manufacturing processes and achieve higher profitability.
6. Siloed systems
Siloed systems are another significant challenge in the manufacturing environment, often leading to the failure of Industry 4.0 digital transformation in manufacturing projects. Siloing refers to the inability to scale digital transformation from individual levels to the entire organization.
The reason behind this is often the presence of varied business goals within an organization, with these goals neither communicated nor understood by all employees. In a business where employees do not feel comfortable sharing ideas or are reluctant to do so, the digital transformation process is likely to fail due to the team’s inability to collaborate effectively.
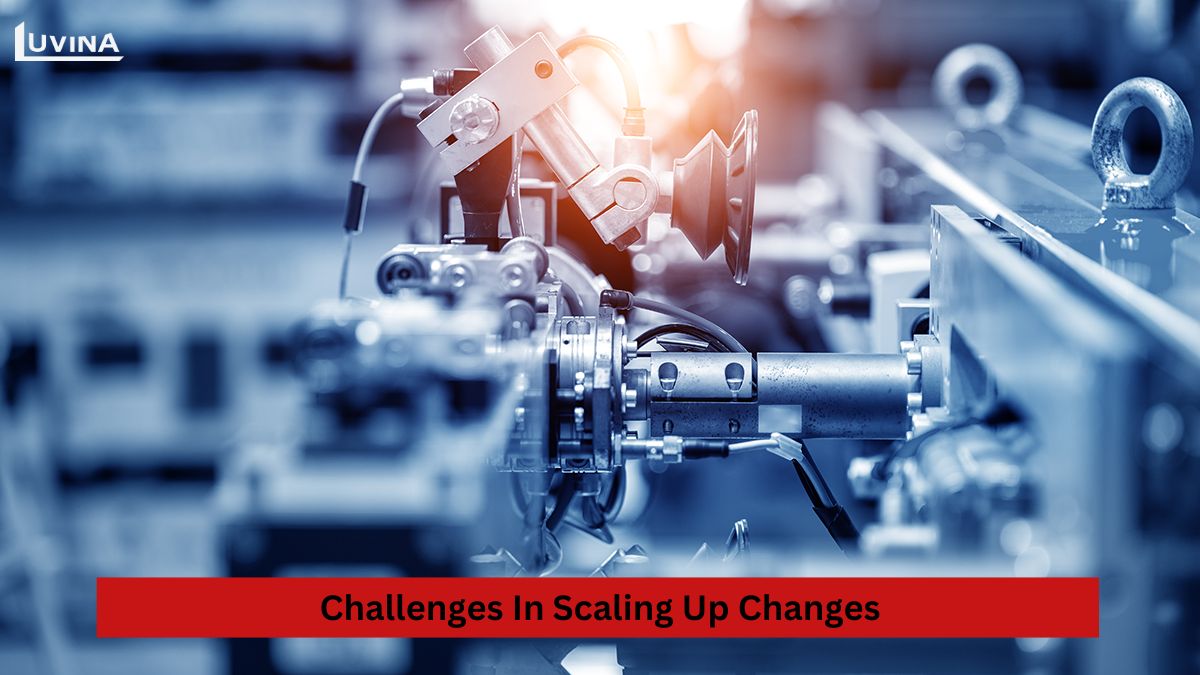
Digital Transformation in Manufacturing: Examples and Use Cases
Each company’s digital transformation in manufacturing is unique, so the methods for implementation and technology applications will differ. Here are some digital transformation examples in manufacturing.
1. Artificial Intelligence (AI) and Machine Learning
AI and machine learning are key drivers of manufacturing and digital transformation, offering various advantages to businesses. With the support of AI and machine learning, manufacturing companies operate smarter, more efficiently, and more safely by automating many repetitive processes. Additionally, this technology enables manufacturers to better predict trends, improve quality control, produce products faster, and reduce waste. Companies adopting digital initiatives in the manufacturing industry use AI and machine learning in various ways. Examples include:
- Predictive Maintenance: AI can predict equipment failures and identify the optimal times for maintenance, reducing operational downtime, lowering maintenance costs, and extending equipment lifespan. Even when you’re not actively monitoring machinery, predictive systems help maintain it in top condition.
- Quality Control: AI is widely used in quality control systems. Paired with computer vision, it can inspect products for imperfections and detect flaws that human workers may overlook, thereby enhancing product quality.
- Demand Forecasting: In digital transformation in smart manufacturing, AI and machine learning also help companies accurately forecast product demand, allowing for better inventory management and more efficient production planning.
There are numerous examples of companies in the manufacturing sector successfully implementing AI and machine learning for smart factory transformation. For instance, BMW’s Car2X technology enables real-time interaction between vehicles and production systems.
>> Read more: AI in Manufacturing Examples & Use Cases
2. IoT sensors
IoT sensors have, therefore, a very important task in manufacturing: taking measurements and monitoring industrial processes. Such devices are deployed either in factories or elsewhere to gather data on the performance of equipment along several metrics including but not limited to oxygen levels, temperature, and pressure. In digital transformation in manufacturing, IoT sensors are typically used for:
- Smart Manufacturing: Advanced digital tools and automation technologies collect real-time data across production lines and provide information about equipment performance, operational efficiency, and energy use; they assist them in data-driven decision-making and help address an issue on time. Smart manufacturing approaches the goal of improving process efficiency, productivity, inventory planning, issue resolution, and minimizing overall costs.
- Supply Chain Optimization: In manufacturing, IoT sensors offer visibility into inventory levels, shipment statuses, and environmental conditions. This transparency enables manufacturers to monitor materials and products throughout the supply chain, ensuring timely delivery and improved logistics.
>> See more: PLM Software for Manufacturing: A Complete Guide
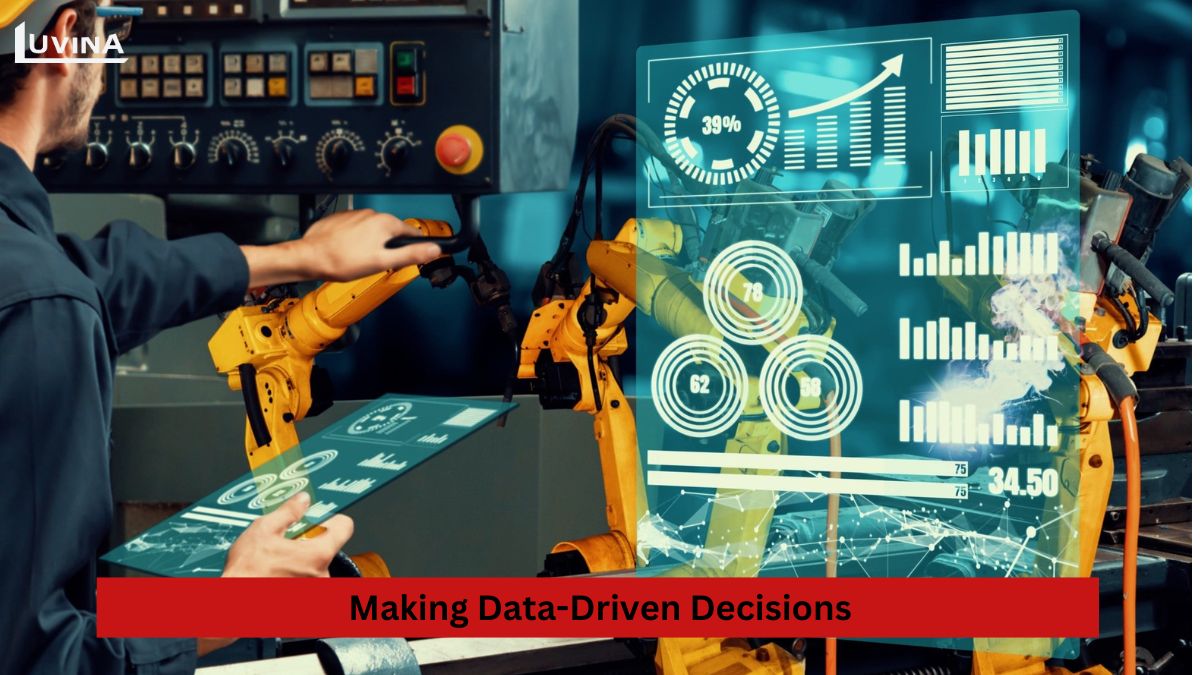
3. Big Data and Analytics
Big Data encompasses the volume, the velocity, and the variety that different companies generate and collect. In digital transformation in automotive manufacturing, big data is called the essential ingredient in the quest for better business performance and efficiency, as it allows manufacturers to identify and take action on trends that are emerging, thus making wiser decisions with regard to business operations and the supply chain.
The analysis of data from the customers can also enable the manufacturer to get insight into their consumer preference, therefore developing products that meet customer demand, improving customers’ satisfaction, and hence an increase in sales.
4. Cloud-based ERP and manufacturing software
The adoption of cloud-based ERP systems or other manufacturing software is one of the major examples of digital transformation in manufacturing. These applications can totally streamline business operations because they safely store data in the cloud, where it can be accessed from any location. This cloud-based ERP lets employees have access to updates on a particular project and information on their mobiles. Besides this, it facilitates support for inventory management, customer relationship management, and so on.
>> Top 7 Best ERP Solutions for Manufacturing Industry
5. 3D printing
3D printing involves making objects from digital designs through layering materials that thicken and become solid shapes. Recently, 3D printing has been one of the most transformational technologies in manufacturing, particularly within industries that deal with very complicated products, such as in aerospace, automotive, and defense. This technology allows the production of rapid prototyping at a low cost, reducing time-to-market. For instance, Boeing has begun flight tests for 3D printing Apache helicopter rotor systems.
6. Augmented Reality (AR) and Virtual Reality (VR)
In the age of digital factory transformation, AR enhances users’ surroundings with computer-generated information, while VR immerses users in a fully digital environment. Both technologies are revolutionizing manufacturing processes by enhancing efficiency. For example:
- Assembly Guidance: AR can display step-by-step assembly instructions on workers’ screens or simulate entire production lines, allowing workers to view finished products virtually before production begins.
- Training: VR immersion provides a controlled learning environment where employees can practice without risks, especially valuable in handling complex machinery.
- Maintenance and Repair: AR applications guide workers through intricate maintenance and repair tasks, helping reduce errors and downtime.
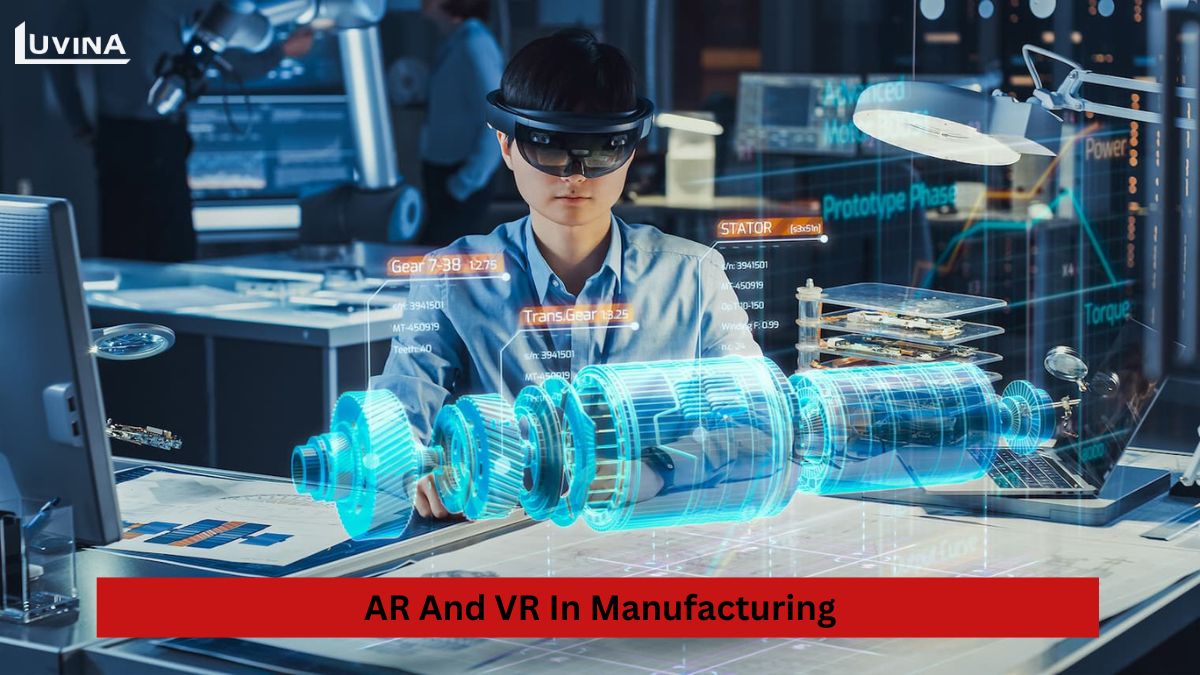
How to Develop a Digital Transformation Strategy for Manufacturing?
In this article, we cannot provide detailed steps for the digital transformation in manufacturing because each business and company needs a customized process. However, to answer the question: Industry 4.0—how to navigate digitization of the manufacturing sector? You must ensure the following when planning a strategy for digital transformation for manufacturers.
- Identify business goals and challenges: Before starting digital transformation in industrial manufacturing, you need to identify your business goals and challenges. Specifically, you need to understand your company’s strengths, weaknesses, opportunities, and threats.
- Build a detailed and suitable digital transformation strategy: Developing a digital transformation in manufacturing market strategy will outline how you will integrate digital technologies into your production activities to achieve business goals. A suitable digital transformation strategy should align with business goals, focus on areas where digital technology can make the most impact, and consider potential risks and methods to manage these risks when deploying digital technologies.
- Ensure readiness of digital infrastructure: The readiness of digital infrastructure includes setting up IT infrastructure that supports the digital technologies you plan to deploy, from hardware and software to network devices.
- Carefully consider the digital technologies to deploy: The next stage is implementing digital technologies to optimize your production activities. You can integrate these technologies into your production lines, supply chain, or other business areas. Some technologies you can adopt include automation and robotics, Internet of Things sensors, AI and machine learning, cloud computing, etc. Each of these technologies will play a different role in the digital transformation of business processes in manufacturing.
- Train the workforce: Training the workforce is essential when building an effective factory digital transformation strategy. Your workforce needs to have the necessary skills to operate and maintain modern production equipment.
Conclusion
Manufacturing digital innovation is significantly changing how production processes are carried out, bringing numerous new opportunities. Not only does smart manufacturing digital transformation increase operational efficiency, but it also reduces costs, optimizes resource allocation, and helps manufacturing companies operate more flexibly.
If you’re aiming to become a pioneer in the digital transformation of the manufacturing sector, contact us to learn how Luvina can support your business in gaining a competitive edge in this constantly evolving field. With over 20 years of IT expertise, we assist manufacturing companies in leveraging suitable technological solutions tailored to their needs. Here are some of Luvina’s core services:
- Workflow Management: We design and implement robust solutions that streamline operations, enhance productivity, and optimize resource utilization.
- Purchase Management: We develop purchase management software with comprehensive features.
- Warehouse Management: Using state-of-the-art technology like cloud computing, we help manufacturing businesses optimize inventory management.
Contact Luvina today for creative and tailored solutions that will set your business on the path of digital transformation in manufacturing.
Read More From Us?
Sign up for our newsletter
Read More From Us?
Sign up for our newsletter